Weld Test Standards
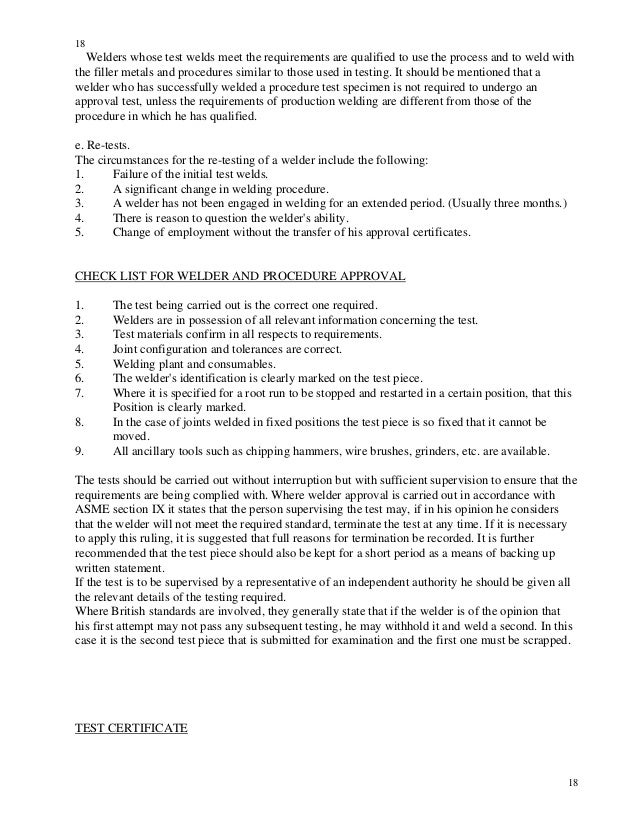
Welding standards cover industry agreed upon conventions like definitions of terms and of symbols as used in the industry for conveying information.
Weld test standards. Simply stated a standard is a document used repeatedly as a rule guideline or definition. With each new individual who discovers a passion for the arc there is a pressing need to develop synchronicity within the industry through the use of standards. Methods for destructive testing of welds in metal method 2 3. Shielded metal arc welding flux cored arc welding self shielded and submerged arc welding the arc welding processes protected by flux along with the gas shielded processes such as gas tungsten arc welding.
Methods for destructive testing of welds in metal part 2 2. Welding recommended practices reflect the recommendations of some of the most knowledgeable professionals in the field with the purpose of helping people improve the practical implementation of. Estone 7 piece fillet weld set gage gauge welding inspection test ulnar mm inch mg11 several pieces of equipment are required for visual weld quality testing. Non destructive weld testing standards cover multiple possible methods of testing welds or metallic materials.
The welding world is growing at an exponential rate. What is a standard. The american welding society aws publishes over 240 aws developed codes recommended practices and guides which are written in accordance with american national standards institute ansi practices. When setting up a new resistance spot welding process optimum parameters must be sought usually using a standard as a guideline and the weld quality must be verified this is done by destructive testing.
Although many standards exist advising the range of parameters that should usually be applied for specific materials. Subject matter covered in actual aws and other welding examinations include. Fillet weld gauge is an essential weld quality testing tool. Specifications approval of welding procedures mechanical testing en iso 15614 1 adopts the same mechanical test as en288 3 except that the bend test minimum former angle has been increased from 120q to 180q and fillet welds require a minimum of 4 macros.
When impact testing is required the minimum thickness has been reduced from 12mm to 6mm. The test may be performed with or without a qualified welding procedure note without an approved welding procedure the welding parameters must be recorded. Methods for destructive testing of welds in metal method 2 2. Non destructive testing analysis techniques are used for qa evaluations research in cases where the product is expensive or unique failure analysis and so on.
The following is a partial list of the more common publications. The requirements for approvals are determined by the relevant application standard or as a condition of contract table 1. Take this free welding practice exam to get a sample of the types of questions on an actual welding exam.